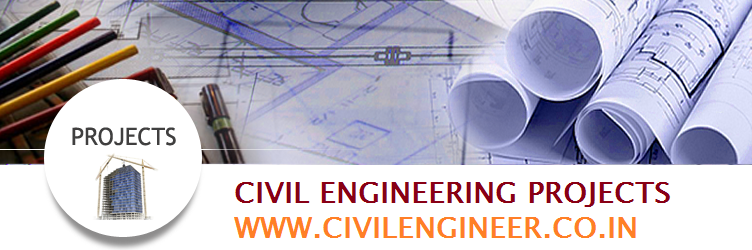
TIME AND MOTION STUDY ON
ROAD CONSTRUCTION TECHNIQUES
Motion and time study can reduce and control costs, improve working conditions and environment, and motivate people.
The basic purpose is to improve the work and to reduce waste.
1. Motion analysis techniques
2. Time study techniques
3. Uses of time standards.
Manufacturing management and engineering students are being prepared to design work stations, develop efficient and effective work methods, establish time standards, balance assembly lines, estimate labor costs, develop effective tooling, select proper equipment, and layout manufacturing facilities.
However, the most important thing is to learn how to train production workers in these skills and techniques so they can become motion and time conscious.
Motion study offers a great potential for savings in any area of human effort. We can reduce the cost by combining elements of one task with elements of another.
Motion study uses the principles of motion economy to develop work stations that are friendly to the human body and efficient in their operation.
Motion study must consider the operator’s safety
Time study can reduce cost significantly well. Time standards are goals to strive for. In organizations that operate without time standards, 60% performance is typical.
When time standards are set, performance improves to an average of 85%. This is a 42% increase in performance:
85 % – 60 %
—————— = 42% performance increase.
60%
Incentive systems can improve performance even further.
Incentive system performances average 120%, that is another 42% increase in performance:
120% – 85%
———————- = 42% performance increase.
85%
Manufacturing plants with no standards average 60% performance.
Manufacturing plants with time standards average 85% performance.
Manufacturing plants with incentive systems average 120% performance.
If additional production output is required, don’t buy more machinery, don’t add a second shift, and don’t build a new plant.
Just establish a motion and time study program.
Motion and time study is considered to be the backbone of industrial engineering, industrial technology, and industrial management programs because the information that time studies generate affects so many other areas, including the following:
1. Cost estimating
2. Production and inventory control
3. Plant layout
4. Materials and processes
5. Quality
6. Safety
Motion study comes first before the setting of time standards. Motion study is a detailed analysis of the work method in an effort to improve it.
Motion studies are used to
1. Develop the best work method.
2. Develop motion consciousness on the part of all employees.
3. Develop economical and efficient tools, fixtures, & production aids.
4. Assist in the selection of new machines and equipment.
5. Train new employees in the preferred method.
6. Reduce effort and cost.
Motion study is for cost reduction, and time study is for cost control. Motion study is the creative activity of motion and time study.
Motion study is design, while time study is measurement.
Once the importance of motion and time study is understood and accepted, the techniques of motion and time study are introduced.
- Flow diagrams
- Multi activity charts
- Operation charts
- Flow process charts
- Process charts
- Operations analysis chart
- Work station design
- Motion economy
- Flow patterns
- Predetermined time standards system (PTSS).
The techniques of time study start with the last motion study technique, which shows the close relationship between motion study and time study. The techniques of time study are:
- Predetermined time standards system (PTSS)
- Stopwatch time study
- Standard data formula time standards
- Work sampling time standards
- Expert opinion and historical data time standards.
WHAT IS A MOTION STUDY?
Motion studies are performed to eliminate waste. Before any improvement in quality or quantity of output, any study of operations time, any scheduling of work or balancing of workload or any calculation of standard time, a study of the current and proposed method is required.
Studies of overall factory flow or process, called macromotion studies, and then additional studies of detail or operations, called micromotion studies, should be completed for a project.
Motion studies were conducted by Frank and Lillian Gilbreth about a century ago in a search for the “one best way.” It is important to note that such studies seek to minimize and simplify manual efforts.
A Study On Resource Planning In Highway Construction Projects
ABSTRACT
The Construction projects, especially the highway construction projects, uses huge amount of resources on and off the field in various forms of resources viz., materials, plants, equipments and human resources along with money, time and space. The uniqueness of the projects makes the resource planning a tedious job as the efficiency of each resource depends upon a huge number of working condition factors. A detailed study of resource planning and productivity can, thus help in good resource planning, better monitoring and overall controlling of the project. In highway projects, the same resource is often used for different activities and the productivity of that resource being different for different activities, it becomes inevitable to know the correct norms for correct estimation, planning and monitoring. The main objective of this thesis work was to planning the main resources (i.e. the equipments, plants and manpower) deployed at a highway project by using Microsoft Soft Project Software. Keywords – BRTS, Resource Planning
1 Introduction
Observing the trend in construction technology presents a very mix and ambiguous picture. On the one hand many of techniques and materials used for construction are essentially unchanged since the introduction of mechanization in the early part of twentieth century. For example at the time of highway construction at the beginning of the nineteenth century most of the highway project report stated that ―the work could not have been done any faster or more efficiently in our days, despite all technological and mechanical advances in the time, since the reason being that no present system could possibly carry the spoil material away any faster or more efficiently then the system employed. No motor trucks were in the digging of soil everything ran on the rails foe cutting and filling of soil at different chainage to reduce the wastage of human resources and achieve maximum productivity. And because of quantity of soil and rain, no other methods have work so well to achieve the desired output.
In contrast to this view of one large project, it may also point to the continuous change an Improvement occurring in traditional material and technique. This continuous improvement in techniques help to plan and distribute the resources as per the requirement and efficient distribution of all these resources helps in close monitoring and actual progress of the work which includes resources like man, material, machinery and money with respect to their productivity.
2 Methodology
- First forecasting input and output is done in which the data wise requirement of project manpower, costly equipment, production costs, sales or earned value of work done and expected income.
- Then the planning the construction work force by determining the size of project work force, its structuring into functional groups and workers team and scheduling manpower recruitment to match task requirement.
- After this plan the construction materials which involves identifying the materials required, estimating quantities, defining specifications, forecasting requirements, locating sources material sample approved, material inventory.
- Then planning construction equipment which aims at identifying the construction tasks to be undertaken by mechanical equipment, assessing the equipment required, exploring the equipment procurement and finally selecting the equipment. Planning the construction standard cost, the cost plan uses standard cost work packages, work items or activities. Then finally plan construction budget which involves structuring of project functional organization into production, services and administration responsibility center, allocating resources with budgeted cost and finally compiling the project financial plan in the form of project master budget.
3 Resource Planning
3.1 Planning Construction Work Force The project man power planning primarily focuses on determining the size of project work force, its structuring into functional groups and workers teams, and scheduling the manpower recruitment to match the task requirement.
This process chiefly involves identifying the trades or the skills required, establishing productivity standards to determine the number of worker needed to perform a given job in the specified time, data wise forecasting of workers requirements for accomplishing the project work and finally organizing the planned work force into operating work-teams having assigned programmed tasks.
3.2 Planning Construction Materials Efficient material management in project environments calls for an integrated approach covering numerous functions such as materials planning and programming, materials purchasing, inventory control, store-keeping and ware housing, materials transportation and handling at site, materials codification and standardization and the disposal of surpluses. The material planning and programming, which is the key function on materials management is closely linked with the project planning and control set-up. Both these work together to develop a plan to procurement and stocking of construction materials so as to provide at site, materials of right quantity, at right prices from right source and at the right time. The construction material planning involves identifying the materials required, estimating quantities, defining specifications, forecasting requirements, locating resources for procurement, getting material samples approved, designing material inventory and developing procurement plan to ensure a smooth flow of materials till the connected construction work are completed at the project site.
3.3 Planning Construction Equipment Production task needing equipment include excavating, handling, transporting, filling, compacting, grading, hoisting, concreting, pre-casting, plastering, finishing, trenching, and laying of pipes and cables. The supporting equipment at project site consists of generators, transmission lines, pumping sets, other utility services equipment. Construction equipment is indispensable in execution of modern high-cost, time-bound massive construction projects. It produces output with an accelerated speed in a limited time. It saves manpower, which is becoming ever more costly and demanding. It improves productivity, quality and safety and also adds a sense of urgency. Acquisition of equipment mass involves initial heavy investment but, on the whole, its ads to profitability by reducing the overall costs, provided it is properly planned, economically procured and effectively managed.
Equipment planning for a project aims at identifying construction task to be undertaken by mechanical equipment, assessing the equipment required, exploring the equipment procurement options and finally, participating in the decision making for selecting the equipment.
hi