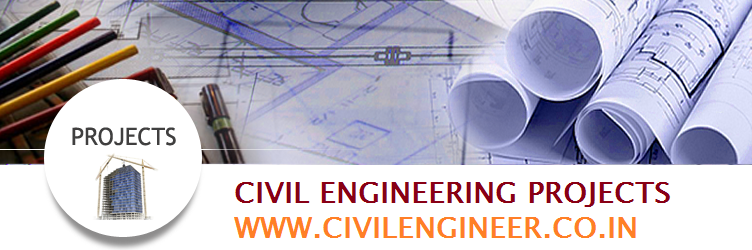
Ferrocement Construction Technology and
its Applications – A Review
Ferrocement construction technology is quite popular throughout the world. Ferrocement, a thin element, is used as a building construction as well as a repair material. This paper attempts to review the literature on ferrocement and bring out the salient features of construction, material properties and the special techniques of applying cement mortar on to the reinforcing mesh. This study brings out the importance of using ferrocement in swimming pools and water tanks, silos, corrugated roofs, shell and dome structures, and also in the repair of old/ deteriorated RCC structures. Also is discussed in this paper a similar material to ferrocement, termed as Engineered Cementitious Composite, which uses fibers as reinforcement. The recommendations of this study include addition of fibers in ferrocement to reduce crack-width. The present authors recommend that experimental investigation may be conducted on new reinforcing materials by researchers in the future. The study concludes that ferrocement will certainly be one of the best structural alternatives for RCC in the future.
Keywords: Cement Mortar, Ferrocement Repair, Fibers, Weld Mesh
1. Introduction
1.1 Ferrocement Technology
Shelter is one of the basic needs of human being. But more than 80 developing countries in the world suffer from housing shortages resulting from population growth, internal migration, war, natural disaster, to mention a few. Most dwellings in rural areas are made of cheap local materials including low quality wood (which is easily attacked by termites), scrap metal, thatch and/or earth products (like clay, mud, sand, rock/ stone) which are temporary and unsafe. There is an urgent need to explore a building material that is structurally efficient but at the same time, should be lightweight, eco-friendly, cost effective and especially the ones that can perform the desired functions (Akhtar et al. 2009). Ferrocement is such a material that is slim and slender but at the same time strong and elegant (Pushyamitra Divekar, 2011) which provides a potential solution to roofing problems (Abdullah and Takiguchi, 2003), with an history of ancient and universal method of building huts by using reeds to reinforce dried mud (wattle and daub) (ACI Committee 549-R97). Small ferrocement tanks of less than 18.9 m3 (5000 gal) capacity were being factory built in New Zealand (Bulletin CP-10, 1968), and elevated water tanks of 47.3 m3 (12500 gal) capacity were successfully constructed in Bangladesh in 1989 (Mansur, 1990). Ferrocement silos can hold up to capacity of 10 metric tons (22400 lb) of grain/ food stuffs, fertilizer, cement and pesticide (Naaman, 2000). Ferrocement is more durable than wood/ timber and cheaper than imported steel (Hago et al. 2005). Small capacity ferrocement bins upto 3 metric tons which are cylindrical in shape, and size of 1.20 m (3.9 ft) in diameter and prefabricated in heights of 1 m (3.28 ft) is analysed and successfully tested in India (Sharma et al. 1979) and the results have proved that ferrocement bins are less expensive than the bins made of steel, reinforced cement concrete (RCC) or aluminium (ACI 549 R97). Two feasibility studies have shown that the cost of ferrocement is less than that of steel or fiberglass in the construction of wind tunnels (Report JABE-ARC-07, 1976) or hot water storage tanks (Report No.E-40-1-4899, 1976). In 1984, a swimming pool of 25 m X 12.5 m (82 by 41 ft) was built of ferrocement in Vila Loma Jlbacoa beach by the Enterprise Beaches of the East of Havana and its deeper part 1.80 m (5.9 ft) depth, with thickness of 25 mm (1 in.) in the walls were formed with precast panels. The total cost was almost seven times lower than one built with RCC of same size (Ferro 10 Information).
1.1.1 Uniqueness of Ferrocement
Ferrocement is a thin construction element with thickness in the order of 10-25 mm (3/8–1 in.) and uses rich cement mortar; no coarse aggregate is used; and the reinforcement consists of one or more layers of continuous/ small diameter steel wire/ weld mesh netting. It requires no skilled labour for casting, and employs only little or no formwork (Ferro 7, 2001). In ferrocement, cement matrix does not crack since cracking forces are taken over by wire mesh reinforcement immediately below the surface (Desai, 2011). Husain Doshi Gufa, an underground ferrocement shell structure which was built in 1993 at Ahmedabad, India has not only withstood the 2001 earthquake but also has remained crack-free till date (Doshi et al. 2011). Such a structure involving complex curvatures can be constructed in a reliable manner using ferrocement technology, giving free reign to architectural expression. Ferrocement construction technology is being popularized throughout the world in countries like Canada, USA, Australia, New Zealand, United Kingdom, Mexico, Brazil, the former USSR, Eastern European countries, China, Thailand, India, Indonesia, and in other developing countries due to its uniqueness and versality (Shannag and Ziyyad, 2007). Ferrocement is being explored as building materials substituting stone, brick, RCC, steel, prestressed concrete and timber and also as structural components—walls, floors, roofs, beams, columns and slabs, water and soil retaining wall structures; other applications include window and door frames and shutters (Divekar, 2011, 2011a,b,c). Ferrocement can be fabricated into any desired shape or structural configuration that is generally not possible with standard masonry, RCC or steel (Robles-Austriaco, 2006; Dongyen et al., 2006; Kondraivendhan & Pradhan, 2009).
1.1.2 Ferrocement Structures World-wide
There are many structures built of ferrocement–housing units, shell roofs, water tanks and swimming pools, biogas digesters, silos, food storage units, and for some specialized applications such as floating marine structures for which reinforced concrete is too heavy, ferrocement is a preferred choice over reinforced concrete (Naaman, 2000; Hago et al., 2005; Abasolo et al., 2009). In the early 1960s, ferrocement construction was widely accepted in Australia, New Zealand, and the United Kingdom. From then on, thousands of ferrocement vessels and structures were built in quite a number of countries. In Israel, ferrocement is used to improve existing houses (Adajar et al., 2006). Ferrocement houses utilizing local materials such as wood, bamboo or bush sticks as equivalent steel replacement have been constructed in Bangladesh, Indonesia and Papua New Guinea. In Sri Lanka, ferrocement houses resistant to cyclones are developed and constructed (Adajar et al. 2006); and corrugated ferrocement sheets have been developed and tested by the Building Research Institute, State Engineering Corporation, Colombo, Sri Lanka; these sheets are developed as a replacement for asbestos cement corrugated sheets which are widely used as a roofing material (Naaman and Shah, 1976; ACI Committee 549R-97). In India, many ferrocement structures implemented by Auroville Centre for Scientific Research (CSR) are testimony of durability of the ferrocement technology (CoP, 1997). Precast ferrocement elements have been used in India, the Philippines, Malaysia, Brazil, Papua New Guinea, Venezuela and the Pacific for roofs, wall panels and fences. Precast corrugated roof units reinforced with local fibers comparable to asbestos cement sheet and galvanized iron sheet are used in Singapore, India, Indonesia, Peru and Zimbabwe (Robles-Austriaco, 1992). In Singapore, highly mechanised techniques have been used to produce water tanks, sunscreens and secondary roofing slabs and cladding materials for facades (Paramasivam, 2011). A large rectangular ferrocement flume 35 m (115 ft) long, 2 m (6.6 ft) wide, and 1.3 m (4.3 ft) high has been built in the hydraulic engineering laboratory at the National University of Singapore to conduct model tests under wave action (Paramasivam et al. 1985). The remarkable work done using ferrocement are acoustic panels of ferrocement hung from ceiling in the de Menil Museum in Houston, Texas and ferrocement permanent formwork gracing the ceiling of the Schlumberger building in Cambridge, U.K. (Ferro 7, 2001).
1.1.3 Engineered Cementitious Composites (ECC)
Similar or equivalent to ferrocement is another material developed by the University of Michigan, called Engineered Cementitious Composite (ECC) which has been prepared using water, cement, sand, fiber, and some common chemical additives; coarse aggregates are not used in this mix as they tend to adversely affect the unique ductile behaviour of the composite; ECC, in general, uses 2% or less (by volume) of discontinuous fibers, even though the composite is designed for structural applications; and ECC has been generally reinforced with Poly-Vinyl Alcohol fibers (PVA) or high modulus Polyethylene fibers (Li and Kanda, 1998). Investigations have also been conducted on ECC at the University of Tokyo, Kajima Corporation, and the Building Research Institute, Tsukuba City in Japan. The properties of ECC include high damage tolerance, high energy absorption; and the ability to deform under shear is considered a superior property of ECC in seismic resistance applications. The difference between ferrocement and ECC is that the former uses wire or weld mesh and the latter uses fibers. In ECC, there is large interaction between the fibers and the cementing matrix, and fibers create many microcracks with a very specific width, rather than a few but very large cracks noticed as in the case of RCC.
1.1.3.1 Applications of ECC
The applications of ECC include short columns, highway pavements, bridge decks and permanent formwork, etc. The 1 km. (0.62 mile) long Mihara Bridge in Hokkaido, Japan was opened to traffic in 2005; and the steel-reinforced road bed contains 800 m3 (28251 ft3) of ECC material; the tensile ductility and tight crack control behaviour of ECC led to a 40% reduction in material used during construction (Technology Network, 2009). Similarly, a 225 mm (9 in.) thick ECC bridge deck on interstate 94 in Michigan was completed in 2005 and 30 m3 (1059 ft3) of material used was delivered on-site in standard mixing trucks (Lepech and Li, 2009). The 95 m (312 ft) Gloria Roppongi high-rise apartment building in Tokyo containing a total of 54 ECC coupling beams (2 per storey) was intended to mitigate earthquake damage; similar structures include the 41-storey Nabeaure Okohama Tower (4 coupling beams per floor) (MRS Bulletin, 2006). A sixty year old dam which was severely damaged showing evidence of cracks, spalling and some water leakage in Mitaka Dam near Hiroshima was repaired using ECC with 20 mm (0.78 in.) thick layer in 2003 (Technology Network, 2009). Also in 2003, an earth retaining wall in Gifu, Japan was repaired using ECC (Li et al. 2009).
1.1.4 Need for Repair of RCC Structures
Although hundreds of thousands of successful RCC structures are annually constructed worldwide, the deterioration of existing RCC structures in many countries necessitates the need for developing cost-effective and long-term repair to use them for their intended service life and to assure the safety of the building (Al-Dulaijan et al., 2002). Repair of damaged RCC structures are successfully carried out using ferrocement to restore the structural integrity, to reshape the defective structures and also to protect the reinforcement from severe weather conditions (Zamin Bin Jumaat et al. 2010). In the early 1980s, Romualdi et al. (1998) and Iorns
(1987a,b) were the first to introduce the ferrocement techniques for repairing mainly liquid retaining structures such as pools, sewer lines, tunnels, etc. Strengthening of RCC beams and columns using ferrocement laminates have received considerable attention from the research community in recent years due to their high mechanical performance and low cost compared to other techniques (Shannag, 2009).
The next section (2.0) reports information based on previous studies as well as on-going research by the present authors on ferrocement construction technology.
2. Previous & On-going Studies
2.1 Constituents of Ferrocement
Ferrocement is a composite thin element which is constructed of building materials–steel reinforcing mesh, cement, fine aggregate (sand) and water (Naaman, 2000; ACI Committee 549R-97; and Nassif and Najm, 2004) and each of these materials are separately described in this section below.
2.1.1 Steel Reinforcing Mesh
Ferrocement uses layers of continuous/ small diameter steel wire/ weld mesh netting (metallic or non-metallic) as reinforcement with high volume fraction of reinforcement (2 to 8%) and the specific surface of reinforcement is considerably higher for ferrocement than for RCC. Also, the reinforcing steel wire mesh has openings large enough for adequate bonding; the closer distribution and uniform dispersion of reinforcement, transform the otherwise brittle mortar into a high performance material distinctly different from reinforced concrete. Skeletal steel rods/wires/strands are used as spacer material and to form the skeleton of the shape of the structure to be built, around which the mesh layers are later attached (Naaman, 2000).
2.1.2 Cement
Portland cement is generally used in ferrocement. But the type of cement should be selected according to the need or environment in which the structure is built, for example ASTM cement Type I-V mentions the strength characteristics of cement and its specific use / application (ACI 549, IR 93). Mineral admixtures, such as flyash, silica fumes, or blast furnace slag, may be used to maintain a high volume fraction of fine filler material as well as to enhance the properties at wet and hardened state.
2.1.3 Aggregate
Only fine aggregate is used in ferrocement. Coarse aggregate is not used in ferrocement. Normally, the aggregate consists of well graded fine aggregate (sand) that passes a 2.34 mm
sieve; and since salt-free source is recommended, sand should preferably be selected from river-beds and be free from organic or other deleterious matter (Sakthivel & Jagannathan, 2011). Good amount of consistency and compactibility is achieved by using a well-graded, rounded, natural sand having a maximum top size about one-third of the small opening in the reinforcing mesh to ensure proper penetration (ACI Committee 549R-97). The moisture content of the aggregate should be considered in the calculation of required water (Naaman, 2000).
2.1.4 Water
In ferrocement, the water used for mixing cement mortar should be fresh, clean and fit for construction purposes; the water of pH equal or greater than 7 and free from organic matter—silt, oil, sugar, chloride and acidic material (ACI Committee 549R-97).
2.2 Ferrocement Construction Process
Construction sequencing/ process is important for ferrocement construction. Since the ferrocement elements are very thin in the order of 10-25 mm (0.39-1 in.), considerable care is to be taken to maintain minimum cover of 3 mm (1/8 in.). The details on storage of materials, details of the workers, tying of reinforcement, preparation and application of mortar and curing are detailed in this section below.
2.2.1 Easy Storage
Not much storage space is required in ferrocement work for storing building materials as compared to traditional construction sites (using RCC) in which large number of cement bags, huge number of bricks, heaps of sand and coarse aggregates, heavy steel reinforcing bars, many steel sheets/plates, timber runners and planks for formwork works and large number of wood/ bamboo or steel pipes for scaffolding purposes are involved (Divekar, 2011b). Since the material such as weld/ wire mesh is available in rolled packs in the market, it can be easily purchased and stored, utilising less space.
2.2.2 Construction Workers
Ferrocement construction requires known skills of normal artisans; three types of workers—steel barbender/ fabricator (to cut and tie the chicken/wire/weld mesh to required sizes), welder (to weld the mesh to the skeletal reinforcement) and mason (for casting purposes) are required to produce the ferrocement components/ elements (Divekar, 2011b). The fabricated and mesh-tied steel bar cage for ferrocement cavity wall of 10 sq.m. (108 sq.ft.) area weighs only 50 kg (110 lb) and can easily be lifted and erected by two persons (Divekar, 2011).
2.2.3 Tying of Reinforcement
As per the design requirements, one or more layers of chicken and/or wire/ weld mesh reinforcement are decided upon. Binding/ tie wires used should be properly cut and bent inwards. It is essential that the wire/weld mesh reinforcement is laid evenly and firmly tied to each other as well as to the skeletal steel, and welding has to be done as per the requirements (Sakthivel and Jagannathan, 2011).
2.2.4 Design of Cement Mortar Matrix
The chemical composition of the cement, the nature of the aggregate (sand), the aggregate-cement ratio, and the water-cement ratio are the major parameters governing the properties of the cement mortar mix (Sakthivel & Jagannathan, 2011). The mortar matrix is designed for its appropriate strength and maximum denseness and impermeability, with sufficient workability to minimise voids and to avoid map cracking; the use of sharp fine grade sand as aggregate together with ordinary Portland cement is generally adequate, despite the low covers employed; this is due to the comparatively high cement content in the mortar mix. Cement mortar used in ferrocement acts as a good insulator and the reinforcing wire mesh can reduce surface spalling better than plain concrete (Vatwong and Pichai, 2008). Precautions are necessary to maintain the small cover and in selection of aggregates, mixing, placing and curing (Paramasivam, 2011). Mortar recommended for ferrocement shall comprise particles or aggregates of limited size. The mortar matrix usually comprises more than 95 per cent of the ferrocement volume and has a great influence on the behavior of the final product. The cement mortar should be mixed with proper sand-cement ratio (ranging from 1.5-2.5 by weight) and water-cement ratio (between 0.35-0.45 by weight) in order to achieve sufficient plasticity and facilitate easy casting (ACI Committee 549-R97). Many defects are possible due to lack of complete infiltration and consolidation. The mix should be as stiff as possible (except when closed moulds are used), provided it does not prevent full penetration of the mesh. Normally the slump of fresh mortar should not exceed 50 mm (2 in.). Mortar absorbs water quicker than it dries out. The ingredients used for mixing cement mortar should be carefully batched by weight, including the water, and added or charged in the mixer so that there is no caking. The water-cement ratio should be as low as possible but the sand-cement ratio should be adjusted to provide a fluid mix for initial penetration of the armature followed by a stiffer, more heavily sanded mix at the finish (Sakthivel and Jagannathan, 2011). For most applications with normal weight concrete and steel meshes, the 28 day compression strength of 75 X 150 mm (3 by 6 in.) moist cured cylinders should be not less than 35 MPa (5000 psi) (Naaman 2000). Since compressive strength and porosity are related, cement mortar of higher compressive strengths upto 70 MPa (10000 psi) are desirable in ferrocement structures like water tanks where improved impermeability and water-tightness are required (Sakthivel & Jagannathan, 2011). Admixtures or additives may be added to improve the performance of the cement mortar, depending upon the type of structures.
2.2.5 Mortar Placement/ Application
In ferrocement construction, mortar plastering and penetration on to the mesh plays a crucial role. The mortar is usually impregnated in the mesh reinforcement either by hand or shot through a spray gun device (shotcreting) in order to get a homogeneous mixture of ingredients and produce almost a fabric of mesh coated and well packed with mortar. Lay-up technique (or laminating process) which was developed by Martin Iorns of California involves placing the mesh in the mortar rather than the mortar in the mesh; and successive layers of mesh are placed in layers of freshly sprayed, or manually placed, mortar. To assure that mesh layers do not pop out, a thin mortar cover layer is placed first and allowed to set, but not dry completely, prior to application of a second mortar layer and the first mesh layers. This first layer of mortar cover is generally about 3 mm (1/8 in.) thick. A major advantage of the lay-up technique is that each layer of mesh is placed under full visual contact; any gap in the mortar is immediately apparent and instantly corrected (Naaman, 2000). But the edges of ferrocement which are normally pressed by hand to get the correct profile are highly susceptible for initiating water penetration and trigger cracking into structure; hence, proper edge shuttering, proper mechanical vibration and ensuring proper cover to meshes are proven to have positive bearing on enhancing durability (Doshi et al. 2011). Also, delamination occurs when ferrocement splits between layers which may be in laminated construction. This may be due to springing back or bridging of the mesh during construction. In many developed countries, mechanized and precast methods of application of cement mortar on to the mesh are adopted. It appears that composite action between the matrix and the reinforcement is more pronounced in ferrocement than in ordinary reinforced concrete (ACI Committee 549 R-97; ACI Committee 549 IR-88 & IR-93). If work is carried out without correct material specification and stringent workmanship, ferrocement structures will miserably fail (Desai, 2011).
2.2.6 Curing
Proper curing is necessary to develop the required properties of the mortar. A curing period of 28 days is suggested; however, at least curing in the first two weeks is essential and should start 24 hours after final application of the mortar to avoid shrinkage cracks (Paramasivam, 2011).
2.3 Properties of Ferrocement
The unique properties of ferrocement are described in detail in this section. Also, the research scope on ferrocement is identified and given in this section by the present authors.
2.3.1 Unique Properties & Research Scope
Ferrocement has a high tensile strength and stiffness and a better impact and punching shear resistance than reinforced concrete, because of two-dimensional reinforcement of the mesh system on a per volume basis (Naaman, 2000); and undergo large deformations before cracking or high deflections before collapse (Naaman, 2000; Moita et al., 2003; Memon & Sumadi,
2006; Patil and Prakash, 2009). High surface area imparts ductile characteristics to ferrocement even though mortar is weak in ductility; hence meshes of both square and hexagonal apertures are adopted (Doshi et al., 2011). Specific surface (which is the contact area of reinforcement per unit volume of matrix) of ferrocement of 25 mm (1 in.) thick is 62,795 mm2/sq.m (9 sq.in./sq.ft) as compared to RCC slab of 100 mm (4 in.) thick whose specific surface is 3,375 mm2/sq.m (0.5 sq.in./sq.ft) The modulus of elasticity of ferrocement with CM 1:2 is comparable with M40 grade concrete and CM 1:3 is of M35 grade concrete, and the compressive strength of cement mortar 1:3 (cement: sand) is about 20 MPa (2900 psi) (Doshi et al., 2011). The major limitation in ferrocement is the percentage of reinforcement; and the reinforcement cannot be increased beyond certain limit; this limitation affects the strength of ferrocement and it cannot be employed where high impact or high load are expected (Patil and Prakash, 2009). Although there is a very extensive range of possible research activities, a few special areas appear important for the full development of ferrocement; these relate to impact resistance, fatigue strength, corrosion, compressive strength with various types of meshes, and strength under multi-axial loading conditions (ACI 549R-97). Only limited research has been carried out on the impact of ferrocement system, especially slab elements (Khan et al. 2005). Research into the properties of ferrocement roof panels is urgently required; research on ultimate and cracking behaviour of thin roof panels needs investigation (Hago et al. 2005). There seems to be less use of structural load carrying elements of ferrocement due to lack of elaborate investigation works on the ferrocement materials and its use as structural elements; one such area that is recommended for investigations on ferrocement elements are its ductility characteristics (Dhasarathan et al. 2009).
2.3.2 Cracking Behaviour of Ferrocement
Ferrocement is characterised by its enhanced resistance to cracking, in comparison to reinforced concrete, cracks in ferrocement are narrower and larger in numbers (Al-Kubaisy and Jumaat, 2000). But if there are continuing overloads or structural settlement, the elements crack and these cracks affect the structural action of ferrocement panels (Adajar et al. 2006), and a replacement or a structural overlay will be required. Delamination sometimes occurs at or near the neutral axis under impact or flexure when there are many voids in the interior layers. Such areas give off a hollow sound when tapped with a hammer or stroked with a steel bar. Pressure from expansive corrosion products may also cause delamination. Spalls (generally depression resulting when a fragment is detached from a larger mass by a blow, by the action of weather, by pressure, or by expansion within the mass) are usually caused by corrosion of steel, which causes an expansive pressure within the ferrocement. Hair line cracks and crazing due to temperature changes or drying shrinkage in the cover coat do not require repair. Cracks due to occasional impact or overload are repairable (ACI Committee 549-R97; ACI Committee IR-88 & IR-93). Biggs (1972) points out that damage must be repaired quickly because, while ferrocement has good resistance to a single impact, repeated impacts at load levels well below the initial impact will pulverize the mortar. A similar danger exists when major cracks are allowed to expand under cyclic loading. Incorporation of fibers in ferrocement panels have contributed significantly in improving the cracking behaviour under flexure (Patil and Prakash, 2009). Different types of fibers made of steel, carbon, glass and polypropylene, that is, either short discrete fibers or continuous long fibers to the cement-based matrix, to improve the properties of cement mortar (Sikdar et al. 2005; Patil and Prakash, 2009). Addition of short and discrete synthetic fibers (like polypropylene, polyolefin, poly-vinyl alcohol, polyethylene) control cracking and increase the capacity of the matrix to resist tensile loads and shear resistance of cement mortar (ACI Committee 549-R97; ACI Committee IR-88 & IR-93).
2.4 Ferrocement Construction Process
As thin structural elements, ferrocement has been used in numerous applications ranging from engineered structures to architectural applications (Paramasivam, 2011) such as sheets, boards, shells, hulls, and also sandwich type construction using thin skins, and constructions where the reduction of self-weight, improved water permeability and development of very fine crack widths are essential (Sakthivel & Jagannathan, 2011).
2.4.1 Structural Applications
Ferrocement can be used in various structural members subjected to different type of stresses. As a compression member, hollow columns with horizontal stiffners can be cast in ferrocement. Columns or walls in concrete, RCC, stone or brickwork can be encased in ferrocement to increase their strength due to confinement. Members subjected to membrane stresses like shells, domes, pyramids can be cast in ferrocement very easily; and being a homogenous material, full section of member is utilized in resisting the membrane stresses. A ferrocement hyperbolic paraboloid shell structure was constructed by the student chapter of the American Society of Civil Engineers at the University of Illinois in Chicago, U.S.A. in 1977 (Naaman, 2000). Funded by the International Development Research Centre of Canada, two proptotype cylindrical water tanks for the collection of rainwater were designed, constructed, and tested for use in the rural areas of the Phillipines (Paramasivam et al. 1990). A greater use could be made of ferrocement in water-retaining constructions and other similar constructions where crack width is a design criterion (Al-Kubaisy and Jumaat, 2000). Because of its very small crack widths under service load and it superior extensibility, ferrocement provides excellent leakage characteristics for applications in water tanks; moreover, should pressure increase, ferrocement stretches to allow higher leakage and acts as a safety valve, thus, it does not fail (Naaman, 2000).
2.4.2 Roofing Applications
Ferrocement appears to be an economic alternative material for roofing; and flat or corrugated roofing system is quite popular (ACI Committee 549-R97). Ferrocement roofing materials can be factory mass-produced in prefabricated form, a process best suited to the concentrated demands of the urban area, or it also can be fabricated in-situ in villages. Construction of hundreds of ferrocement roofs for poorer areas of Mexico has been well documented; most of these ferrocement roofs were dome shaped with a span of 3 to 6m (10 to 20 ft); and large ferrocement roofs have also been constructed in Italy spanning 17m (56 ft) with a thickness of30 mm (1.2 in.). The use of ferrocement as roofing for large span structures with internal ribs has been successful in many European and South American countries. Domes have been constructed in Jordan using 25 mm (1 in) thick ferrocement with internal ribs (Jennings, 1983).
2.4.3 Need for Repair of RCC Structures
Some major reasons for the deterioration of RCC structures are cracking (due to incorrectly made construction joints, poor compaction, segregation, poor curing and high water content) and spalling (due to corrosion in the reinforcement bars accelerated by a lack of adequate cover). The cracks in the concrete may be developed due to wrong design of structure or due to poor quality of materials used, and this will facilitate internal corrosion of steel reinforcement used in RCC elements; the cracks in course of time deepens up due to increase in corrosion and subsequently, peeling of concrete cover or spalling of concrete takes place. Use of proper repairing materials and methods of damaged or deteriorated RCC structures is a necessity not only to serve the intended service life but also assure the safety of buildings (Masood et al. 2003).
2.4.4 Ferrocement Repair Techniques
A good repair improves the function and performance of structures, restore and increase its strength and stiffness, enhances the appearance of the concrete surface, provides water tightness and prevents ingress of the aggressive species to the steel surface durability (Jumaat et al., 2006). Ferrocement repairs and rehabilitation can be done in RCC structures to increase the strength of columns, beams and slabs upto 30% as well as contribute towards prevention of crack formation. Ferrocement which can be made from non-formwork construction processes is an advantage over other types of repair and strengthening techniques; enhanced crack resistance combined with high toughness, its rapid constructions with no heavy machinery involved, small additional weight it imposes, and considering an economical aspect of rehabilitation, this material proves to be a cost effective solution for rehabilitation and general applications (Jeyasehar and Vidivelli, 2006). The ferrocement material is a waterproof system and does not allow the penetration of water and atmospheric gases. It can totally replace deteriorated/ damaged RCC chajjas with reduction in dead load.
2.4.4.1 Ferrocement Repair Methodology
It is generally noticed that corrosion of RCC structures most commonly takes place in the main reinforcement in slabs, beams and columns and the stirrups, where proper cover is not maintained and where reinforcement is exposed in the cover area. Patchwork repair can be done using ferrocement to the damaged concrete surfaces in slabs, beams and columns to restore the original strength of the RCC. Ferrocement patch repair method can be carried out in columns, bottom and middle portions of beams, soffit of slabs, etc. and following are the repairing steps recommended in the previous studies (Vidivelli et al. 2001; Banu and Taranju, 2010; Zamin Bin Jumaat et al., 2010):
Step 1: Breaking open the damaged spalled cover or the affected zone or the cover of RCC elements (such as beams or columns) with the help of a chisel and hammer.
Step 2: Exposing the original reinforcing bars and scraping of corrosive layers of reinforcement and applying anti-corrosive paints (if any) or cutting and replacing the corroded reinforcement
Step 3: Roughening the concrete surface, and placing chicken and/or galvanised wire/ weld mesh in position and the mesh should get fixed/ embedded to original slab/beam/column reinforcement. Use skeletal reinforcement, if required.
Step 4: Applying cement mortar on the reinforcing wire-mesh by hand or through spraying (similar to guniting/ shotcreting methods)
Step 5: Provide necessary curing for 28 days.
Alternatively, ferrocement membrane protective layer can be carried out. In this, layers of closely spaced wires can be used on to the RCC surfaces to prevent crack widening. The cement matrix is in proportion of about 1:2 and has admixtures which reduce shrinkage and develop early high strength. The matrix is vibrated locally using light vibrating tools. Finish of the membrance is just like plaster.
2.4.4.2 Ferrocement Confinement
Ferrocement confinement is done around defective circular or square/rectangular RCC columns in order to enhance the strength, ductility and energy absorption capacity of existing concrete columns. A jacketing layer of 30 mm (1.2 in.) is created alround the RCC columns with ferrocement is done in order to increase its load carrying capacity. This confinement work also protects the existing reinforcement, provides water tightness and prevents ingress of the aggressive species to the surface of original concrete or steel surface. Ferrocement not only increases the performance/ function of structures but also enhances the appearance of the existing RCC structure. The repair in the structural elements using ferrocement can withstand for long years without cracking provided the mortar used is of proper proportion using good quality materials, and the wire mesh is of anti-corrosive coating type (Masood et al., 2003).
3. Recommendations of this Study
Based on the comprehensive review of literature, the following are the inferences drawn by the present authors:
1. Ferrocement is an innovative material and has a number of structural applications which includes earth-retaining walls, swimming pools, underground and overhead water tanks, where water-tightness is a requirement. Ferrocement is also used in construction of corrugated roofs, hyperbolic paraboloid shell structures, domes and housing structures. Ferrocement thin
elements are used in facades, sunscreens and curtain walls, and the architectural beauty and grandness of the building is enhanced due to its sleek nature.
2. This study recommends ferrocement as the best alternative material to RCC and also a construction material of the future due to its following properties/ advantages:
• Ferrocement elements undergo high deformations before collapse. It has high level of impact and cracking resistance, toughness and ductility.
• The ferrocement structures are thin and light-weight compared to conventional reinforced concrete. Hence there is considerable reduction in self-weight of the structure and saving in foundation cost. Transportation cost is also less.
• Ferrocement can be fabricated into any desired shape or configuration. Precasting is suitable for thin ferrocement elements, and mechanised methods can be adopted in case of mass production of ferrocement components.
• Partial or complete elimination of formwork is possible. Hence there is considerable saving in the cost of formwork, particularly for curved or complicated/ complex shapes/ structures, which is not possible with RCC construction.
• Ferrocement construction is simple and quick and does not require highly skilled labour; and the labourers can also be easily trained for this job. Also it does not require any heavy equipment / machinery for casting or lifting purposes. It is an economically feasible material and also suitable for developing countries in both urban and rural areas.
• Due to less consumption of building materials and scaffolding items in ferrocement, (as compared to RCC), not much space is required for storing materials.
• Ferrocement is most suitable for water-retaining structures due to water-tightness and impermeability.
• Ferrocement structures can be easily maintained, and also repaired in the event of structural damage without any major problems.
3. This study recommends ferrocement as a repair material due to the following reasons:
• Ferrocement is suitable for repair works in boats, water tanks, swimming pools, sewer lines etc. Ferrocement is also suitable for repair or rehabilitation/restoration of ancient or heritage building structures. The repaired elements can withstand long years without cracking.
• Ferrocement repair to old/deteriorated RCC structure is cheaper and quicker than demolition of such structures and reconstructing them. Ferrocement patch repair techniques help in easy bonding of old and the new layers, and patches also do not show up in ferrocement as the layers easily merge with each other.
• Less or no formwork construction processes is involved in ferrocement repair methodology.
4. This study is of the opinion that ferrocement jacketing method of confining reinforced concrete columns is one of the most suitable methods to enhance its load-carrying capacity and strength.
5. Few suggestions of this study on ferrocement are that care should be taken to mix the cement mortar and apply to the reinforcing mesh as per the required technical specifications, and more emphasis should be paid in selection of a richer cement-sand ratio and lower water-cement ratio for the ferrocement mortars, as specified by the ACI Codes.
6. As there are only limited studies on corrosion in ferrocement, it is recommended by the present authors, that in order to prevent corrosion, new meshes manufactured of stainless steel, plastic, PVC, or any other non-metallic mesh reinforcement may be explored as reinforcement in ferrocement. But the structural load carrying capacity and other characteristics of these elements, using such new materials, are to be ascertained through experimental studies.
7. This study also recommends that fibers may be added as additional reinforcement in ferrocement into the matrix composition for crack-control and resistance against local loads. Synthetic fibers (such as nylon, poly-vinyl chloride, polyolefin, polyvinyl alcohol, polyethylene and polypropylene) can be used in ferrocement instead of steel fibers so as to avoid corrosion.
8. In order that ferrocement is to become an accepted building material, this study strongly recommends that considerable research on new reinforcing materials should be done. The two different concepts of ―Ferrocement using Wire/ Weld Meshes‖ and ―Engineered Cementitious Composite using Discontinuous Fibers‖ can be combined and a new material may be developed to provide a hybrid composite with improved properties. Experiments may be conducted on such ferrocement composite elements to study the flexure, impact and punching, ductility, and cracking behaviour of ferrocement elements.
4. Conclusion
This study has brought out that ferrocement is an innovative material and the ready availability of materials and ease of construction make it suitable in developing countries for housing, and water and food storage structures. Ferrocement is found to be a suitable material for repairing or reshaping the defective RCC structural elements and enhancing its performance. The applications of ferrocement are capturing almost all the fields of civil engineering but there is a dirth of research backing and a rationale design base to construction of ferrocement structures. As the performance of ferrocement is greatly dependent on the characteristics of the reinforcing mesh, there is a need to determine and specify an optimum range of properties for the mesh, such as wire spacing, wire diameter, and the characteristics of the mesh system. This is only a review study and experimental research on new building materials for use in ferrocement construction or combinations of meshes and fibers are needed. The standard methods of ferrocement construction and effect of shape due to which novel forms are generated have to be researched upon and benefits brought out. Considering the unique features, ferrocement will no doubt be one of the most important structural alternatives for RCC and a repair material in the future and thus has a great potential for developing and developed countries alike.
Ferrocement:
Ferrocement is a building material composed of a relatively thin layer of concrete, covering such reinforcing material as steel wire mesh. Because the building techniques are simple enough to be done by unskilled labor, ferrocement is an attractive construction method in areas where labor costs are low. Sand, cement, and water usually can be obtained locally, and the cost of the reinforcing material (steel rods, mesh, pipe, chicken wire, or expanded metal) can be kept to a minimum. There is no need for the complicated formwork of reinforced cement concrete (RCC) construction, or for the welding needed for steel construction. Virtually everything can be done by hand, and no expensive machinery is needed.
Additional advantages of ferrocement construction:
- Ferrocement can be shaped in any form.
- It can be formed into sections less than 25 mm (1 inch) thick and assembled over a light framework.
- The material is very dense, but structures made from it are light in weight.
- It is also rot- and vermin-proof, impervious to worms and borers, and watertight.
- Ferrocement is more versatile than RCC and can be formed into
simple or compound curves. In contrast, RCC construction is cast
in sections and needs extensive and very solid formwork to support
the weight of the concrete. - It is a strong, versitile, low-cost, long-lasting building material made from a wire reinforced mixture of sand, water, and cement. A ferro-cement structure is usually 2-5 cm (3/4″-1 3/4″) thick— much thinner and lighter than poured concrete structures. Because it has wire reinforcing distributed throughout the structure, ferro-cement structures have much greater tensile strength and flexibility than ordinary concrete.
-
More advantages at a glance are follows:
o It is highly versatile and can be formed into almost any shape for a wide range of uses;
o Its simple techniques require a minimum of skilled labor;
o The materials are relatively inexpensive, and can usually be obtained locally;
o Only a few simple hand tools are needed to build uncomplicated structures;
o Repairs are usually easy and inexpensive;
o No Maintenance is necessary;
o Structures are rot-, insect-, and rat-proof, and non-flammable;
o Structures are highly waterproof, and give off no odors in a moist environment;
o Structures have unobstructed interior room; and
o Structures are strong and have good impact resistance.
In Third World countries, ferrocement is almost always economically competitive with steel, wood, or glass-fiber reinforced plastic (FRP) construction, because steel and FRP are expensive and wood is becoming more and more scarce. Because its use for construction requires locally available materials and a large supply of hand labor, local jobs can be created.
What are the disadvantages of ferrocement?
- Structures made of it can be punctured by forceful collision with pointed objects.
- In corrosive environments (for example, sea water) it is often
observed that after several decades the reinforcing materials
become corroded. - Fastening with nails or by welding is not possible.
- The large amount of labor required for ferrocement construction
is a disadvantage in countries where the cost of unskilled or
semi-skilled labor is high. Tying the rods and mesh together is
especially tedious and time consuming. - The main disadvantage of ferrocement for smaller structures and boats is its high density (2400 kg/[m.sup.3], 150 pounds/cubic foot). Density is not a problem, however, for larger structures (for example, large domes, tanks, and boats over 12 m long). Large, internally-unsupported domes and curved roofs have been built that could not have been constructed with other materials without elaborate ribs, trusses, and tie rods.
Some Applications
Ferrocement’s features make it useful in a wide range of applications, including aqueducts, boats, buildings, bus shelters, bridge decks, concrete road repair, factory-built homes, food and water storage containers, irrigation structures, retaining walls, sculptures, and traffic-caution signboards.
The least desirable designs for ferrocement construction are those that have large flat surfaces combined with angles of 90 degrees or less. However, non-bearing walls, artitions, dock floats and septic tanks, with or without internal or external stiffening, have been successfully constructed. Large, flat-bottomed barges can also be built with ferrocement in combination with precast RCC frames and girders.
HISTORY:
The use of ferrocement as a boat-building material was demonstrated by the Italian ngineer and architect Pier Luigi Nervi in 1945, when his firm built the 150-metric ton motor sailer Irene. The hull was only 35 mm thick, and was reinforced with three layers of 6-mm (one-quarter inch) rods. Four layers of mesh were used on each side of the rods. The hull weighed five percent less than a comparable wooden hull, and the price (at that time) was 40 percent less. The Irene proved to be a seaworthy vessel, with very little maintenance, and survived two serious accidents that required only simple repairs.
By the early 1960s, ferrocement had gained wider acceptance as a construction material, especially in boat building. After 1970, production slowed because of the rising costs of materials and, especially, labor. Ferrocement construction, however, continues to offer unlimited possibilities for uses both on water and land in places where labor costs are low.
APPLYING MORTAR
Mortar is made from a good grade of Portland cement, well-graded sharp sand, clean water and, optionally, small amounts of additives to achieve an earlier setting strength or for plasticizing. A rich mortar is used in ferrocement construction. The ratio of cement to sand should be 1:2 by weight.
The sand used in the mortar should be clean, dry, and sharp; 10% to 15% should pass through a #100 mesh sieve (opening 0.149 mm), and 100% through a #8 sieve (opening 2.38 mm).
Only fresh water should be used for mixing.
The ratio of water to cement should be 0.45:1 by weight if the sand is perfectly dry; otherwise it should be 0.40:1.
CURING
Curing reduces shrinkage and increases strength and water tightness.
The accepted alternative is to cover the structure, after all the mortar has been applied, with gunny sacks, tar paper, or other fabrics, which are kept moist continuously. Sprinklers or soaker hoses can also be used for this purpose. This procedure must be carried out for at least 14 days. It is desirable not to let the temperature fall below 68 [degrees]F (20 [degrees]C) during the curing process.
FINISHING AND PAINTING
After curing, the surface is rubbed down with abrasive (carbide) stone to achieve a smooth finish, and then rinsed thoroughly with fresh water. Because well-made ferrocement is impermeable (waterproof), there should be no need for painting. However, if painting is desired, the structure should first be scrubbed with a 5%
to 10% solution of hydrochloric acid (HCl; protect eyes and skin), flushed with clean, fresh water, and scrubbed again with a weak solution of caustic soda (NaOH; protect eyes and skin), after which it must be rinsed again.
The ferrocement can then be sealed with a coat of epoxy resin, and one or more coats of epoxy paint applied as a finish. Underground ferrocement grain silos are waterproofed with bitumen.
Reference Book:
Ferrocement: Applications in Developing Countries, by a National Academy of Sciences panel, 1973, National Academy of Sciences, Washington, D.C., out of print.
“Ferrocement is a highly versatile form of reinforced concrete made of wire mesh sand, water, and cement, which possesses unique qualities of strength and serviceability. It can be constructed with a minimum of skilled labor and utilizes readily available materials. Proven suitable for boat-building, it has many other tested or potential applications in agriculture, industry, and housing.
“Ferrocement can be fabricated into almost any shape … is more durable than most woods and much cheaper than imported steel, and it can be used as a substitute for these materials in many applications …. Ferrocement construction does not need heavy plants or machinery; it is labor-intensive.”
Basic technique for making ferrocement pots so far:
Begins with a very basic armature made of the most workable guage of steel for the size of the project. It can be made of 1/8 – 1/4 inch diameter wire/rod for small to medium pots. For pots of a larger size, rebar would be used. Welding makes it quick and easy, but with the right design, wiring would be fine. This sketch is the bare minimum and could be a lot more elaborate, depending on the shape you want to create. We did try a small pot with no armature just 2 layers of chicken wire – it worked but was kind of wiggly, making applying the first layer of cement more difficult.
Wrap with 2 layers of chicken wire. Tie to armature with 17 guage electric fence wire and twist tight with pliers.
The cinsistency of the mix is key.
Add to a wheelbarrow:
3 shovels of sand, 1 shovel of type s masonry cement. 3 times for a total of 9 sand 3 masonry.
mix the sand and cement powder with a hoe. add the perlite (9 shovels). (dust mask good idea)
add water, in small quantities from a bucket, mixing from one side of the dry ingredients to the other. For this purpose, the cement has to be plenty wet to work easily and be sticky, but not so wet as to run or fall off the armature. Add fibers and mix thouroughly and give it some vigorous strokes. It will seem almost fluffy.
Heavy duty rubber dipped gloves are a wonderful tool for this purpose. The key is to get them on both sides of the wire and squeese and spread the cement into the wire in an upward stroke.
An upward motion with both hands helps the gloves to slide over the cement rather than sticking. Resist the temtation to work the cement too much or it will try to fall off. leave a rough surface to help the second coat to stick.
Keep the first coat wet overnite- wrap with damp rags and plastic, and apply second coat the next day. This coat is smoothed with any technique you come up with. rags, sponges, plastic work for smoothing
Ferro-Cement: One material for many uses
If you are thinking about building a low-cost, long lasting water tank, a commercial fishing boat, a life-size model dinosaur, a semi-subterranean house, or a retreat center in the remote desert, ferro-cement might just be your material of choice.
It has been for others. Ferro-cement construction has been used successfully for all of these things.
Other uses for ferro-cement are numerous: walls, floors, and roofs for underground structures, underground water tanks, built-in-place well liners, water control devices, canal lining, retaining walls, stairways built over adobe blocks, rain splash protection for adobe and rammed earth structures —just to name a few.