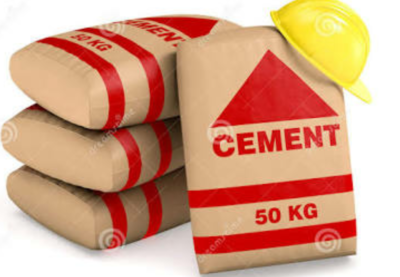
Indian Cement Industry – Background
The Cement Industry in India is over a 100 years old and due to its constant growth and high energy prices, uses the best available technologies in the sector. Most of the large cement plants in India can be characterised as modern with efficient production processes and strict environmental norms. In the early 1990s, Ordinary Portland Cement (OPC) was the most widely produced cement in India, while PPC shared smaller portions of the market. Due to the increased availability of fly ash and new policies that allowed an easier incorporation of the materials in cements, flyash based PPC cornered around 70% of the share of the market with OPC and PSC taking approximately 20% and 10% of the market respectively.
Most of the clinker production units in India are located in seven clusters located around large limestone deposits. Large grinding units also have come up close to coal-fired thermal power plants near urban centers taking advantage of the easy availability of fly ash and high demand of cement in the area. A typical cement plant in India produces 1 to 3 million tones of cement every year. It has been reported that the cost of putting up such a cement plant in India is of the order of 100 to 300 million American dollars. While, due to the recent spurt in construction of new cement plants, the current capacity utilization of the industry strands at around 70%, it is expected that more investment in to the construction of new plants will be required to keep pace with the demand projected in the near future.
The typical cost of production of clinker in a large cement plant in India stands between 1,100 and 1,600 Indian Rupees per tonne. While at most locations, fly ash is available at a cost of 300 to 800 Indian Rupees per tonne, including transportation to the cement plants, at some locations, the landed cost of fly ash can be as high as 1,200 Indian Rupees per tonne. The cost of cement in the market is in the range of 5,500 and 6,500 Indian Rupees per tonne. High excise and tax rates are often cited as the reason behind the price of cement in the market. More than 60% of the cement produced in India is sold in 50 Kilogramme bags and is consumed in the housing sector.
Lime stone makes the majority of the raw material used to produce cement in India. Since Indian limestones generally contain relatively higher levels of siliceous impurities, little to no clay is used in the production of grey clinker in India. As limited amounts of natural gypsum are available in India, cement plants widely use phosphor-gypsum and marine gypsum. Some plants also import high-purity natural gypsum from Oman, Iran, Bhutan etc.
Most plants use the dry process and consume coal, pet-coke and lignite as fuels for the rotary kilns, pre calciners and captive power plants that supply electricity to the plants. Waste heat recovery (WHR) is commonly used to produce electricity in the plants and the exhaust gases are at temperatures as low as 80 degree C. A variety of grinding systems such as ball-mills and vertical roller mills are in use for the grinding of the product. While flyash is generally interground with clinker and gypsum at most plants, some plants use dry air blending systems.